Knapp Testing & Manual Inspection – What Do You Think?
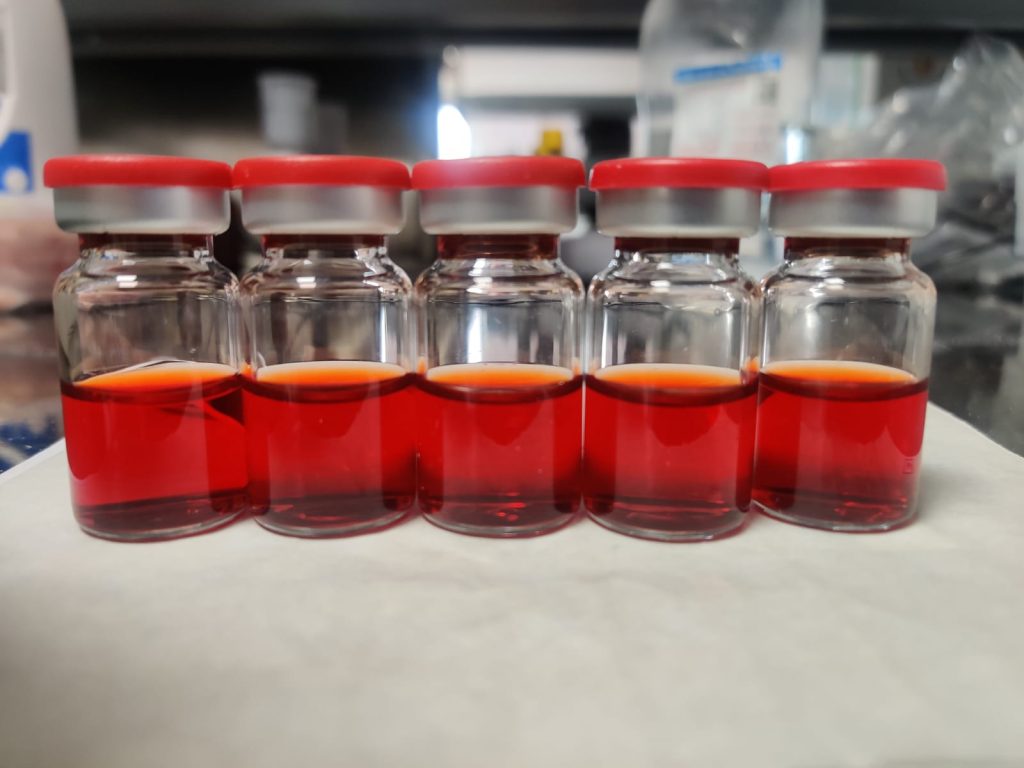
Have you ever come across the words like “Knapp testing” and “manual inspection”? If you’re involved in manufacturing or quality assurance processes, you have heard them. Well, the question is: which one of these approaches is more useful? In this post, we will discuss the answer to this question by understanding and comparing both terms.
Knapp Testing:
Knapp testing is a unique method used in detecting flaws or defects in products. It is based on a systematic approach. The testing involves submitting the item under test to diverse environmental or operation parameters to verify its resistance, reliability, and performance. Employing this approach is particularly common for those industries where product failure could have severe consequences, for example, aerospace, automotive, and medical manufacturing.
Following Knapp testing, products are put under simulated real-world environments like extreme temperature, humidity, pressure, or mechanical strain. Through hardened testing cycles, manufacturers often determine where the components might fail and thus, prevent such from reaching the market. Through this measure – it is possible to improve the quality, reliability, and safety of your products, which results in higher customer satisfaction and brand reputation.
Manual Inspection:
Unlike Knapp testing, manual inspection is done by visually examining products or parts to detect faults, inconsistencies, or deviations from quality standards. While Knapp testing is a process of testing the products by applying stress on them, manual inspection uses human skills to detect an issue that cannot be detected with automated processes.
Manual inspection is mostly applied side by side with other quality control methods such as automated testing and statistical analysis. It allows the inspectors to detect the defects that the automated system cannot capture and offers valuable feedback for process improvement. So, even with the development of automation, manual inspection is still an integral part of many businesses, especially those making items that are complicated or custom-made.
Knapp Testing vs. Manual Inspection
Now, the question arises: Which methodology – Knapp testing or manual quality check – is more efficient? It’s not a clear-cut answer, since the methods have their own pros and cons.
Knapp testing goes beyond utilizing exhaustive testing programs uncovering and highlighting any structural deficiencies and potential failure points. It provides quantitative information that allows manufacturers to design the product better and improve manufacturing processes.
Knapp testing helps to avoid structural failures by revealing potential weak spots using strict testing procedures. The data also offers a predictive tool to manufacturers for optimizing product design and production processes. However, the Knapp test can be too time-consuming and costly for complex products or systems. And it might be replaced by other tests.
On the other hand, manual inspection possesses flexibility and an adaptable nature, allowing inspectors to grasp the intricate defects that the automatic systems cannot sense. Furthermore, the experience and expertise of human inspectors afford qualitative assessments – an assistance to ongoing improvement initiatives. But, human intervention is still subjective and error-prone, resulting in non-consistent inspection criteria.
Make the Right Balance:
In today’s highly manufacturing environment, the right application of both Knapp testing and manual examination is essential. Where Knapp testing provides sensitively obtained data for localizing structural weaknesses, manual inspection adds a human perspective to quality control resulting in the best products.
Therefore, the best way would be to incorporate Knapp testing, manual inspection, and automated quality control systems in an overall quality assurance system. By emphasizing the strengths of these methods, manufacturers can ensure top-quality products, reliability, and customer satisfaction.
Wrapping Up
So, both Knapp testing” and “manual inspection” are complementary steps crucial for product testing. While during Knapp testing products go through extreme testing, manual inspection has the advantage of the human judgment-based expertise to detect minor issues and imperfections. If you want to adopt this strategy that combines the advantages of both technologies, we are at your service. With our world-class services and solutions, we ensure that manufacturers maintain a competitive advantage and produce products that exceed customer expectations.